The reasons for bearing overheating include:
① lack of oil; ② too much oil or too thick oil; ③ dirty oil, mixed with impurity particles; ④ shaft bending ⑤ incorrect transmission device correction (such as eccentricity, transmission belt or coupling If it is too tight, the pressure on the bearing will increase, and the friction will increase); ⑥ The end cover or bearing is not installed properly, and the assembly process is improper, causing the raceway surface to be damaged and deformed, causing friction and heat during operation; the fit is too tight or too loose; ⑦ The shaft Influence of current (because the stator magnetic field of large motors is sometimes unbalanced, an induced electromotive force is generated on the shaft. The reasons for the unbalanced magnetic field are corrosion of the local core, increased resistance, and uneven air gaps between the stator and the rotor, resulting in shaft The current causes eddy current heating. The shaft voltage of the shaft current is generally 2-3V) ⑧ The heat dissipation conditions are poor due to air cooling.
SKF motor bearing failure analysis, maintenance and countermeasures should be based on reasons ①-③. The oil level should be checked and adjusted appropriately; if the oil deteriorates, clean the bearing chamber and replace it with qualified oil.
For reason ④, the bent shaft should be placed on the lathe for verification.
For reasons ⑤-⑥, the diameter and axial alignment should be corrected and adjusted appropriately.
For reason ⑦, the shaft voltage should be measured first, when measuring the shaft voltage. You can use a 3-1OV high internal resistance variable current voltmeter to measure the voltage v1 between the two ends of the motor shaft, and measure the voltage v2 between the base and the bearing. In order to prevent eddy currents in the motor bearings, an insulating plate is placed under the bearing seat at one end of the main motor. At the same time, insulating plate covers are added to the bolts, pins, oil pipes and flanges at the bottom of the bearing seat to cut off the eddy current path. The insulation board cover can be made of cloth laminate (tube) or glass fiber laminate (tube). The insulating pad should be 5~1Omm wider than the width of each side of the bearing base.
For reason ⑧, the ventilation conditions for motor operation can be improved, such as installing fans, etc.
The rolling elements and raceway surface are strained. The bearing generates sliding friction resistance due to sliding during rotation. The interaction of the inertial force and sliding friction resistance on the bearing rollers and cage under high-speed operation causes the rolling elements sliding on the raceway. And the raceway surface is strained.
There are many reasons for fatigue peeling of bearing rolling elements. Excessive bearing clearance, extended use of the bearing, and defects in the bearing material itself can all lead to rolling element peeling. The heavy load and high speed state of bearings during long-term use is also one of the important reasons for bearing fatigue. The rolling elements continuously rotate and slide in the inner and outer ring raceways of the bearing. Excessive clearance causes the rolling elements to bear high-frequency and high-intensity impact loads during movement. In addition, the material defects of the bearing itself and the extended use of the bearing will cause Causes fatigue peeling of bearing rolling elements.
Corrosion Bearing corrosion failures are relatively rare. Generally, it is caused by the failure of the bearing end cover bolts to be tightened in place, causing water to enter the motor during operation, and the lubricant to fail. The motor will not run for a long time, and the bearings will also become corroded. Cleaning rusted bearings with kerosene can remove rust. The cage is loose
A loose cage can easily lead to collision and wear between the cage and the rolling elements during operation. In severe cases, the cage rivets may break, causing deterioration of lubrication conditions and causing the bearing to become stuck.
Reasons for abnormal noise in motor bearings and analysis of the causes of "squeaking" noise from the cage: It is caused by vibration and collision between the cage and the rolling elements. It may occur regardless of the type of grease. It can withstand large torque, load or radial clearance. are more likely to occur. Solution: A. Choose bearings with small clearance or apply preload to the bearings; B. Reduce the moment load and reduce installation errors; C. Choose good grease.
Continuous buzzing sound "buzzing...": Cause analysis: The motor emits a buzzing-like sound when running without load, and the motor undergoes abnormal axial vibration, and there is a "buzzing" sound when turning on or off. Specific features: multiple engines have poor lubrication conditions, and ball bearings are used at both ends in winter.
Temperature rise: Specific characteristics: After the bearing is running, the temperature exceeds the required range. Cause analysis: A. Too much grease increases the resistance of the lubricant; B. Too small clearance causes excessive internal load; C. Installation error; D. Friction of sealing equipment; E. Creeping of bearings. Solution: A. Select the correct grease and use the appropriate amount; B. Correct the clearance preload and coordination, and check the operation of the free end bearing; C. Improve the accuracy and installation method of the bearing seat; D. Improve the sealing form. The motor frequently generates vibration, which is mainly caused by unstable vibration caused by axial vibration when the shaft alignment performance is not good. Solution: A. Use grease with good lubrication performance; B. Add preload to reduce installation errors; C. Select bearings with small radial clearance; D. Improve the rigidity of the motor bearing seat; E. Enhance the alignment of the bearing.
Paint rust: Cause analysis: Because the paint oil on the motor bearing casing dries, the volatile chemical components corrode the end face, outer groove and groove of the bearing, causing abnormal noise after the groove is corroded. Specific features: The rust on the bearing surface after being corroded is more serious than on the first surface. Solution: A. Dry the rotor and casing before assembly; B. Lower the motor temperature; C. Choose a model suitable for paint; D. Improve the ambient temperature where the motor bearings are placed; E. Use suitable grease. Grease oil causes less rust, and silicone oil and mineral oil are most likely to cause rust; F. Use vacuum dipping process.
Impurity sound: Cause analysis: Caused by the cleanliness of the bearing or grease, an irregular abnormal sound is emitted. Specific characteristics: the sound is intermittent, irregular in volume and volume, and occurs frequently on high-speed motors. Solution: A. Choose good grease; B. Improve the cleanliness before grease injection; C. Strengthen the sealing performance of the bearing; D. Improve the cleanliness of the installation environment.
High frequency, vibration sound "click...": Specific characteristics: The sound frequency changes with the bearing speed, and the surface waviness of the parts is the main cause of the noise. Solution: A. Improve the surface processing quality of the bearing raceway and reduce the waviness amplitude; B. Reduce bumps; C. Correct the clearance preload and fit, check the operation of the free end bearing, and improve the accuracy of the shaft and bearing seat. installation method.
The bearing feels bad: Specific characteristics: When holding the bearing with your hand to rotate the rotor, you feel impurities and blockage in the bearing. Cause analysis: A. Excessive clearance; B. Improper matching of inner diameter and shaft; C. Channel damage. Solution: A. Keep the clearance as small as possible; B. Selection of tolerance zones; C. Improve accuracy and reduce channel damage; D. Selection of grease.
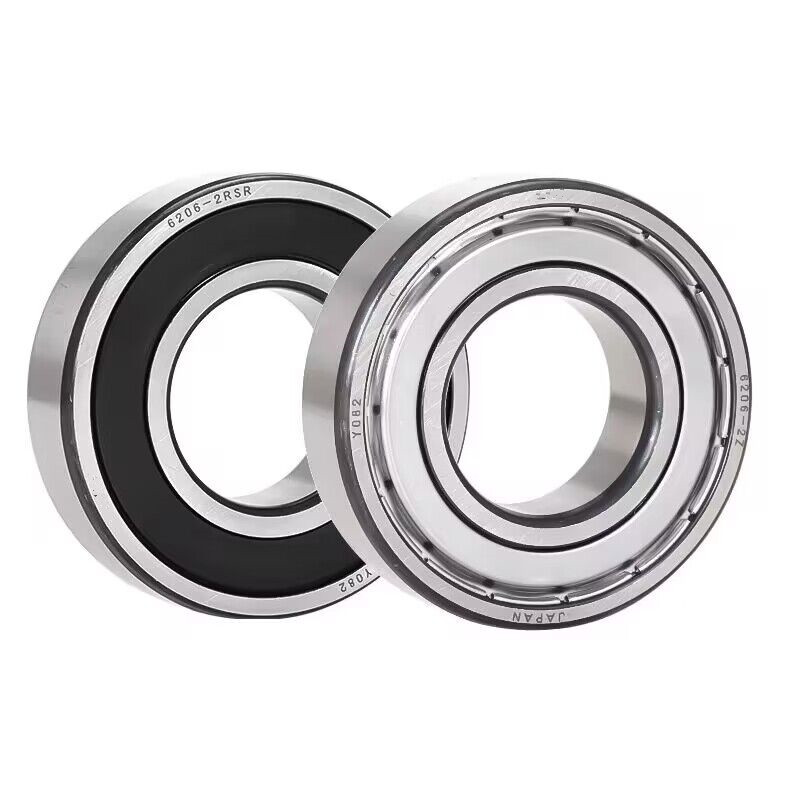
Post time: Jan-02-2024